Choosing between vacuum filtration and centrifugation depends on your specific requirements. Each method offers unique advantages based on performance, cost, and maintenance. Vacuum filtration works well for separating solids from liquids, while centrifugation excels in high-speed separation tasks. Understanding your application ensures you select the most effective solution.
Key Takeaways
- Vacuum filtration works well to separate solids from liquids fast. It is great for larger particles and costs less to maintain. This makes it useful in industries like medicine and food production.
- Centrifugation is better for separating tiny particles and mixtures. It is often used in science labs and cleaning oil. It costs more at first, but it is very accurate and worth the price.
- Pick the method that fits your needs best. For cleaning oil, use a Centrifugal Oil Filtration Machine for tiny dirt. Use a Vacuum Dehydration Oil Purifier to remove water and gas.
Performance Comparison
Efficiency of Vacuum Filtration
Vacuum filtration is highly efficient for separating solids from liquids. This method uses a vacuum to pull the liquid through a filter, leaving the solid residue behind. Studies show that vacuum filtration can achieve efficiency rates of 65% to 99%, depending on the material and conditions. For example, respirators like the 3M™ 8200 achieved a recovery efficiency of 96.5% after vacuum drying.
Study | Efficiency Rate | Notes |
---|---|---|
N95 Masks after vacuum treatment | ≥ 95% | Masks returned to near initial efficiency after treatment |
3M™ 8200 respirator | 96.5 ± 0.2% | Full recovery after vacuum drying following water soaking |
This method works best when you need to process large volumes of liquid quickly. It is also effective for applications requiring high levels of purity.
Efficiency of Centrifugation
Centrifugation relies on centrifugal force to separate components based on density. This method is particularly effective for separating fine particles or emulsions that are difficult to filter. Centrifugation operates at high speeds, which allows it to handle tasks that vacuum filtration cannot. For instance, it excels in separating biological samples, such as blood plasma, or in industrial applications like oil purification.
You might find centrifugation more suitable when dealing with materials that require precise separation or when working with small sample sizes. Its efficiency depends on the speed and duration of the process, as well as the density differences between the components.
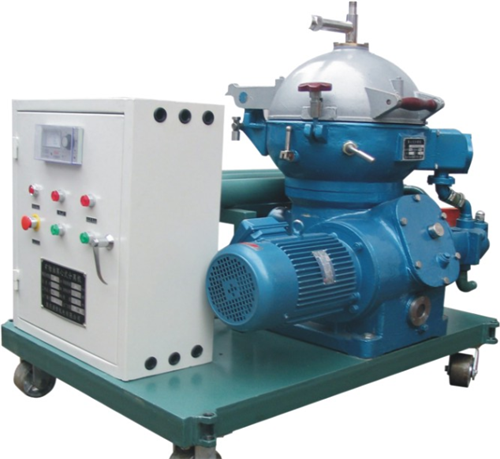
Centrifugal Turbine Oil Purifier
Particle Size and Moisture Removal
The choice between vacuum filtration and centrifugation often depends on the size of the particles and the level of moisture removal required. Vacuum filtration is better for larger particles and applications where complete moisture removal is not critical. On the other hand, centrifugation can handle smaller particles and achieve higher levels of moisture removal.
For example, in oil purification, centrifugation can remove fine contaminants and water more effectively than vacuum filtration. However, vacuum filtration remains a reliable option for simpler tasks, such as filtering sediments from liquids.
Cost and Maintenance
Initial Investment for Vacuum Filtration
Vacuum filtration systems offer a cost-effective solution for many industries. The initial investment is relatively low compared to centrifugation systems, and the return on investment (ROI) is impressive. Studies show that vacuum filtration equipment can extend the life of oil-wetted components by three times the baseline. It also increases oil life by controlling water and removing oxidation by-products, reducing pump failure rates by 67%. For example, Vacuum Facility No. 5 documented annual savings of $12,954, with the equipment paying for itself in less than a year. This makes vacuum filtration an attractive option for organizations seeking long-term savings.
Initial Investment for Centrifugation
Centrifugation systems require a higher upfront investment. Prices range from $1,000 to $50,000, depending on the features and specifications. Industrial-sized models designed for specific applications typically cost between $10,000 and $50,000. Smaller labs and organizations may find these costs prohibitive, especially if their budgets are limited. However, the precision and efficiency of centrifugation often justify the expense for industries requiring high-speed separation or handling fine particles. While the initial cost is significant, the long-term benefits can outweigh the investment for applications demanding advanced separation capabilities.
Maintenance Requirements for Both Methods
Maintenance plays a crucial role in the overall cost of filtration and centrifugation systems. Vacuum filtration systems generally have lower maintenance requirements. They consume less energy and experience minimal wear and tear, making them more economical over time. In contrast, centrifugation systems demand regular upkeep due to their high rotational speeds and exposure to abrasive materials like sludge. Frequent maintenance and parts replacement increase operational costs. Despite these expenses, centrifugation systems can offset their maintenance costs through savings in energy efficiency and operational performance. Choosing the right system depends on your budget and the frequency of use.
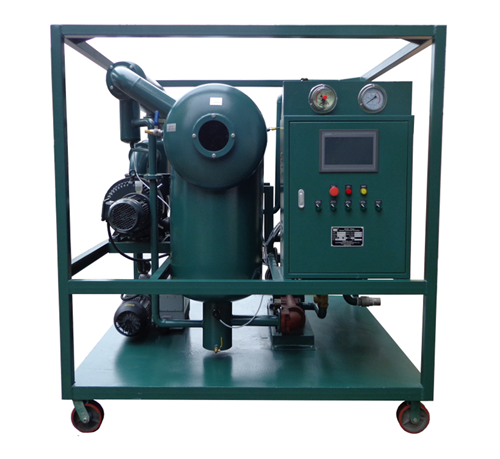
Transformer Oil Purification System
Application Suitability
When to Use Vacuum Filtration
Vacuum filtration is ideal for applications requiring fast and efficient separation of solids from liquids. You can rely on this method when processing materials with larger particles or when complete moisture removal is not critical. Industries like pharmaceuticals, food processing, and chemical manufacturing often use vacuum filtration for its speed and simplicity.
- Key Considerations:
- The thickness and porosity of the filter cake influence the vacuum level needed. For thick filter cakes, absolute vacuum levels of 300 mbar are necessary, while porous cakes require only 600 mbar.
- Water ring pumps are commonly used to maintain the vacuum, ensuring consistent performance.
This method works best when you need to process large volumes quickly, especially in scenarios where maintaining a high filtration rate is essential.
When to Use Centrifugation
Centrifugation is the go-to method for separating fine particles or emulsions that are challenging to filter. You should consider this technique for applications requiring precise separation, such as in biotechnology, oil purification, or blood plasma separation.
Understanding metrics like RPM (Revolutions Per Minute) and RCF (Relative Centrifugal Force) is crucial for optimizing centrifugation processes. These metrics ensure efficient separation, especially in industrial applications where performance indicators like quality and safety are critical. International standards mandate the use of quality indicators (QIs) to monitor and guide centrifugation processes, making it a reliable choice for specialized tasks.
Centrifugal Oil Filtration Machine Applications
Centrifugal oil filtration machines excel in industries where removing fine contaminants and water from oil is essential. These machines are widely used in:
- Automotive and Heavy Machinery: They help maintain engine efficiency by removing sludge and water from lubricants.
- Power Generation: They ensure turbine oils remain clean, reducing wear and tear on equipment.
- Marine Applications: They purify fuel and lubricating oils, enhancing the performance of ship engines.
Brands like ZANYO offer advanced centrifugal oil filtration machines designed to meet these specific needs, ensuring high efficiency and reliability.
Vacuum Dehydration Oil Purifier Applications
Vacuum dehydration oil purifiers are perfect for applications requiring the removal of water and gas from oils. These purifiers are commonly used in:
- Transformer Maintenance: They extend the life of transformer oils by removing moisture and oxidation by-products.
- Hydraulic Systems: They improve system performance by maintaining oil purity.
- Industrial Equipment: They reduce maintenance costs and extend the lifespan of machinery.
Performance studies show that vacuum dehydration oil purifiers can reduce maintenance costs by up to 30% and extend oil life by two to three times. With a payback period of less than two years, these purifiers offer a cost-effective solution for industries aiming to enhance production efficiency.
Pros and Cons Summary
Advantages and Disadvantages of Vacuum Filtration
Vacuum filtration offers several benefits, making it a popular choice in many industries. You can rely on this method for its simplicity and cost-effectiveness. It works well for separating solids from liquids, especially when processing large volumes. Additionally, vacuum filtration systems consume less energy and require minimal maintenance, reducing long-term operational costs.
However, this method has limitations you should consider:
- Traditional mathematical models demand precise measurements of filter cake microstructure, increasing costs and equipment requirements.
- Numerical simulations for vacuum filtration are time-consuming, making real-time control challenging.
- Machine learning algorithms used to predict filter cake moisture content often lack accuracy, limiting their practical application.
These drawbacks highlight the need for careful evaluation before choosing vacuum filtration for complex or high-precision tasks.
Advantages and Disadvantages of Centrifugation
Centrifugation stands out for its efficiency and precision. This method excels in separating fine particles and emulsions, making it ideal for applications like biotechnology and oil purification. You’ll find centrifugation particularly useful when dealing with materials requiring high-speed separation. Its performance indicators further demonstrate its advantages:
Indicator | Centrifugation Performance | Other Technologies Performance |
---|---|---|
Energy Consumption | 50% less energy | Higher energy consumption |
Solids Concentration | 4-5% | 4-5% (requires polymer) |
Volume Reduction | 95% | 80% |
Operational Efficiency | Higher capacity | Limited capacity |
Despite these benefits, centrifugation has its downsides. The initial investment is significantly higher than vacuum filtration. Maintenance costs also add up due to the wear and tear caused by high rotational speeds. These factors make centrifugation less suitable for small-scale or budget-conscious operations.
Both vacuum filtration and centrifugation offer unique benefits. You should choose based on your material type, budget, and industry requirements. For oil purification, a Centrifugal Oil Filtration Machine works best for fine contaminants, while a Vacuum Dehydration Oil Purifier excels at removing water and gas. Brands like ZANYO provide reliable solutions tailored to these needs.
FAQ
What is the main difference between vacuum filtration and centrifugation?
Vacuum filtration separates solids from liquids using a vacuum, while centrifugation uses centrifugal force to separate components based on density. Each suits different applications.
Which method is better for oil purification?
Centrifugation works better for removing fine contaminants and water. Vacuum filtration is more effective for simpler tasks like sediment removal.
💡 Tip: Choose based on your oil type and contamination level.
Are these methods environmentally friendly?
Both methods can reduce waste and improve resource efficiency. Centrifugation uses less energy, while vacuum filtration minimizes chemical usage.