A vacuum dehydration oil purification machine is a specialized device designed to enhance the quality of industrial oils. It removes contaminants like water, air, and solid particles, ensuring the oil remains clean and efficient. This process plays a vital role in maintaining the performance of machinery and extending the lifespan of lubricants.
Vacuum dehydration achieves remarkable results, reducing water content to as low as 10 PPM and filtering particles as small as 1 micron with 99% efficiency. By eliminating free, entrained, and dissolved gases, it ensures oil purity for critical applications.
Key Takeaways
- Vacuum dehydration machines clean oil by removing water, gas, and dirt. This improves oil quality and helps machines work better.
- These machines help equipment last longer by reducing damage. This means fewer breakdowns and cheaper repairs.
- Cleaning oil often makes machines work well and stay clean. It also meets industry rules for cleanliness.
- Buying these systems helps the environment by reusing clean oil. It also cuts down on waste.
- When picking a machine, think about the oil type, size, and features. This ensures it works well with your needs.
What is a vacuum dehydration oil purification machine?
Definition and purpose
A vacuum dehydration oil purification machine is a device designed to remove water, gases, and solid impurities from industrial oils. It uses advanced technologies like vacuum pressure and heating to ensure oil remains clean and efficient. This machine plays a critical role in maintaining the performance of machinery by improving oil quality and extending its usability.
By reducing water content to as low as 20 PPM and achieving ISO-standard particle counts, these machines ensure optimal oil performance across various industries.
Why oil purification is essential
Oil contamination can lead to significant problems in industrial equipment. Water, air, and solid particles in oil cause wear and tear, reduce efficiency, and increase maintenance costs. Purifying oil ensures:
- Extended Equipment Life: Clean oil minimizes wear on machinery components.
- Improved Performance: High-quality oil enhances operational efficiency.
- Cost Savings: Reducing contamination lowers repair and downtime expenses.
Studies show that vacuum dehydration can extend oil life and prevent unscheduled breakdowns, making it a cost-effective solution for industries.
Key components of the machine
A vacuum dehydration oil purification machine consists of several essential components, each serving a specific function:
Component | Functionality |
---|---|
Vacuum Pump | Creates the vacuum environment necessary for the dehydration process. |
Heater | Raises the oil’s temperature to increase vapor pressure of contaminants. |
Filter | Removes solid particles from the oil to maintain its dielectric properties. |
Dehydrator | Absorbs water vapor from the oil to ensure thorough drying. |
These components work together to achieve high water extraction rates and maintain oil purity. Many machines also feature digital temperature controllers and alarm indicators for efficient and safe operation.
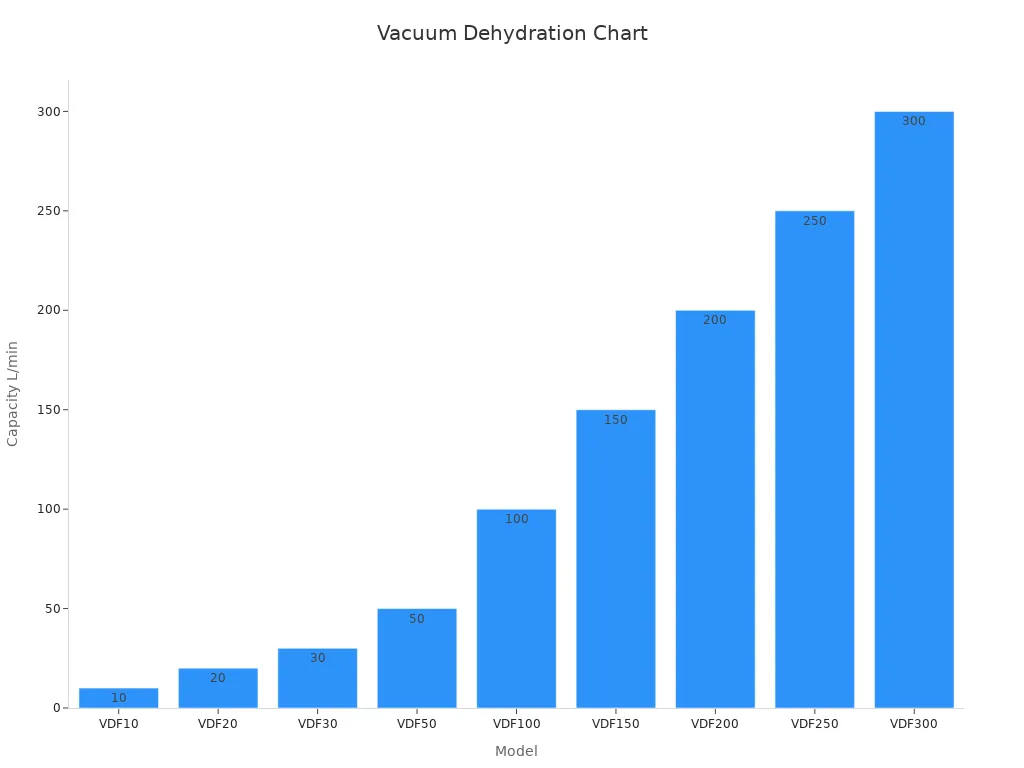
How does a vacuum dehydration oil purification machine work?
Overview of the vacuum dehydration process
Vacuum dehydration is a highly effective method for purifying oil by removing water, gases, and impurities. This process leverages the principle of reducing the boiling point of water under vacuum conditions, allowing moisture to evaporate at lower temperatures. By combining vacuum pressure, heating, and filtration, the machine ensures oil purity and enhances its performance.
The process operates continuously, maintaining high efficiency and reliability. Machines are designed to handle extended working hours, with some models capable of running for over 100 hours without interruption. This ensures consistent oil purification, even in demanding industrial environments.
Metric | Value |
---|---|
Filtration precision | ≤1 micron |
Continuous work | 100 hr |
No failure running | ≥5000 hr |
Power supply | 208V/220V/380V/400V/415/440V/460V/480V/575V (+/-10%), 50/60Hz, 3Phase |
Working noise | 65 dB |
Heating power (kw) | 24, 30, 35, 60, 90, 120, 140, 150 |
Total power (kw) | 27, 33, 40, 65, 100, 130, 150, 165 |
Weight (kg) | 300, 350, 400, 500, 800, 1000, 1200, 1300, 1350 |
Dimension (mm) | L: 1100-2000, W: 800-1350, H: 1200-2000 |
Steps involved in removing water, gas, and impurities
The vacuum dehydration process follows a series of precise steps to ensure thorough oil purification:
- Initial Filtration: The oil passes through an incoming filter to remove solid contaminants.
- Heat Application: The machine heats the oil to facilitate the vaporization of water and gases.
- Vacuum Dehydration: A vacuum pump creates a low-pressure environment, lowering the boiling point of water and extracting moisture.
- Degasification: Dissolved gases are separated from the oil using a distillation column.
- Final Filtration: The purified oil undergoes a final filtration stage to eliminate any remaining impurities.
These steps ensure the oil achieves optimal cleanliness and performance. For example, a substation using a skid-mounted purifier significantly reduced moisture and gas levels, improving the dielectric strength of its transformer oil.
Technologies used in the machine, such as vacuum pressure, heating, and filtration
Vacuum dehydration machines incorporate advanced technologies to achieve superior oil purification:
- Vacuum Pressure: This technology removes dissolved water and gases by creating a low-pressure environment. It is particularly effective when water content in oil systems increases.
- Heating: Heating enhances the vaporization of water, making the dehydration process more efficient.
- Filtration: High-precision filters remove solid particles, ensuring the oil meets ISO cleanliness standards.
These technologies work together to deliver exceptional results, making vacuum dehydration a preferred method for oil purification.
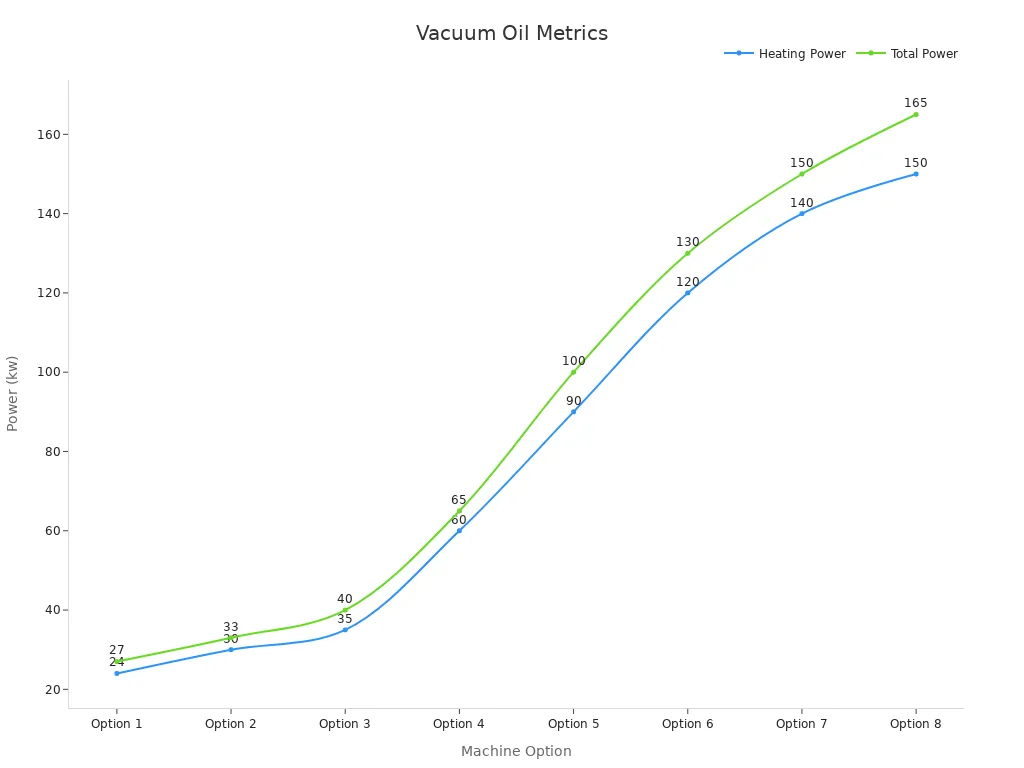
Benefits of using a vacuum dehydration oil purification machine
Extending the lifespan of equipment
Using a vacuum dehydration oil purification machine significantly enhances the durability of your machinery. Clean oil reduces wear and tear on components, ensuring smoother operations and fewer breakdowns. Regular maintenance with purified oil prevents damage caused by contaminants like water and solid particles. This proactive approach extends the lifespan of your equipment, saving you from costly replacements.
Evidence Description | Key Benefit |
---|---|
Regular maintenance prevents wear and tear | Extends machinery lifespan |
Proper lubrication improves durability | Enhances functionality |
Optimizing operational parameters boosts efficiency | Increases operational life |
By maintaining optimal lubrication and operational parameters, you ensure your machinery operates efficiently for years.
Improving oil quality and performance
Vacuum dehydration machines improve oil quality by removing water, gases, and impurities. This process ensures the oil meets industry standards, enhancing its performance in critical applications. For example, reducing water content to below 10 ppm and achieving a particle count of less than 10 particles/ml ensures optimal cleanliness.
Metric | Description | Target Value |
---|---|---|
Water Content Test | Measures the amount of water in the oil. | Ideally below 10 ppm |
Particle Count Test | Counts the number and size of solid particles. | Less than 10 particles/ml |
Dielectric Strength Test | Assesses the oil’s ability to withstand voltage. | Typically exceeding 70 kV/mm |
Purified oil enhances machine performance, leading to higher productivity and a safer work environment. Cleaner oil also reduces the risk of operational issues, ensuring consistent and reliable performance.
Reducing maintenance and operational costs
Investing in oil purification reduces maintenance expenses and operational costs. Cleaner oil minimizes wear on machinery, leading to fewer repairs and less downtime. Regular maintenance with purified oil also decreases the frequency of oil changes, saving on replacement and disposal costs.
- Regular maintenance reduces repair costs significantly.
- Proper scheduling minimizes downtime, enhancing efficiency.
- Cleaner oil extends machinery lifespan, preventing costly breakdowns.
- Oil purification systems lower fluid purchase and maintenance expenses.
By maintaining oil cleanliness, you avoid unexpected failures and ensure smooth operations. This cost-effective solution not only saves money but also boosts overall productivity.
Enhancing environmental sustainability
Vacuum dehydration oil purification machines (VDOPS) play a crucial role in promoting environmental sustainability. By purifying and reusing industrial oils, these machines help reduce waste and minimize the environmental impact of oil disposal. You can rely on these systems to support eco-friendly practices while maintaining operational efficiency.
One of the most significant benefits of using VDOPS is their ability to reduce oil waste. Instead of discarding contaminated oil, you can purify and reuse it multiple times. This approach not only conserves resources but also prevents harmful pollutants from entering the environment. Cleaner oil also ensures that your machinery operates efficiently, reducing energy consumption and lowering your carbon footprint.
Environmental regulations are becoming increasingly stringent. Industries must now maintain high levels of oil cleanliness to comply with these rules and avoid penalties. VDOPS help you meet these requirements by delivering purified oil that meets or exceeds industry standards. Additionally, the growing demand for renewable energy sources has increased the need for clean oils. These machines ensure that oils used in renewable energy systems remain uncontaminated, supporting the global shift toward sustainable energy solutions.
The following table highlights key factors driving the environmental benefits of VDOPS:
Evidence Type | Description |
---|---|
Environmental Regulations | Stringent regulations require industries to maintain high oil cleanliness. |
Renewable Energy Demand | Clean oils are essential for renewable energy systems. |
Contamination Awareness | Awareness of oil pollution drives demand for purification systems. |
By adopting VDOPS, you contribute to a cleaner environment. These machines reduce oil-related pollution, conserve natural resources, and align your operations with global sustainability goals. Their use reflects a commitment to protecting the planet while ensuring long-term industrial efficiency. 🌍
Applications of vacuum dehydration oil purification machines
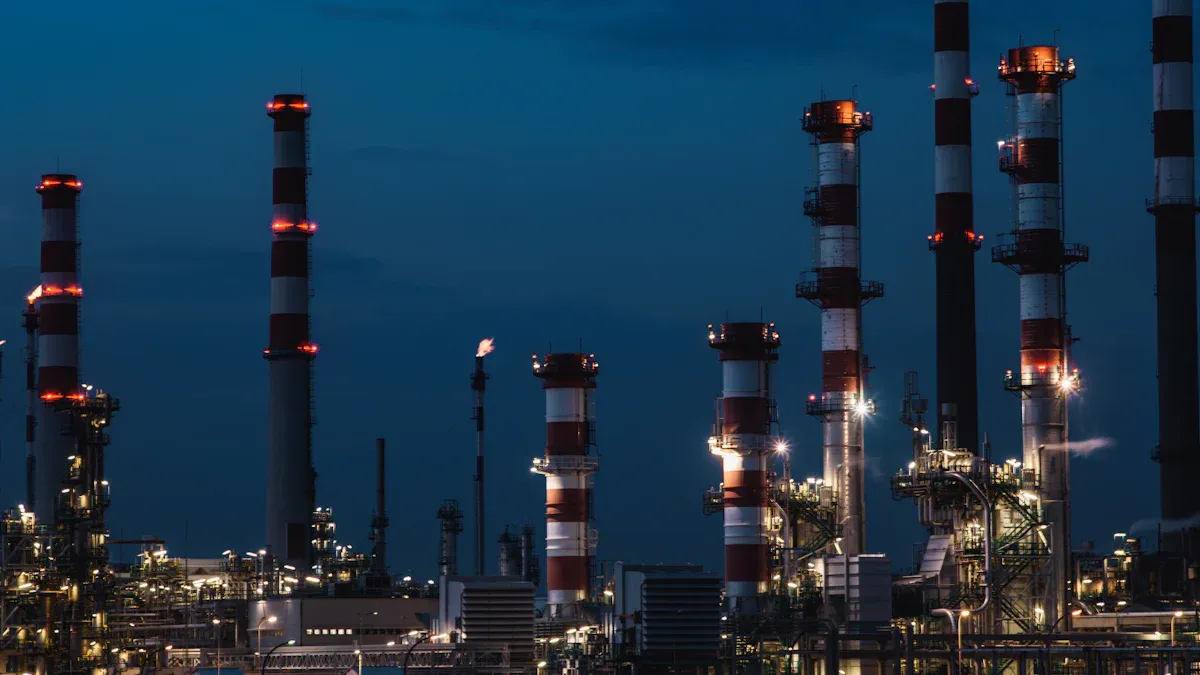
Power generation and transformer maintenance
Vacuum dehydration oil purification machines play a critical role in the power generation sector. They ensure the purity of transformer oils and turbine lubricants, which is essential for maintaining equipment reliability. Contaminated oil can lead to equipment degradation, causing costly downtime and operational inefficiencies. By removing water, gases, and impurities, these machines enhance the performance and lifespan of transformers and turbines.
For example, a substation transformer faced severe oil contamination. Using a skid-mounted purifier restored the oil’s quality, extended the transformer’s life, and reduced maintenance costs. Similarly, a wind farm deployed a portable purifier during an emergency, preventing downtime and safeguarding operations.
The adoption of vacuum dehydration systems is growing rapidly. The market, valued at USD 2.4 billion in 2023, is projected to reach USD 4.8 billion by 2032, driven by industrialization and rising global energy demands. These systems are now essential in thermal, nuclear, and renewable energy plants, ensuring efficient and reliable power generation.
Manufacturing and industrial machinery
In manufacturing, clean oil is vital for maintaining the efficiency and safety of industrial machinery. Vacuum dehydration systems remove contaminants that can cause mechanical failures, reduce productivity, and increase operational costs. By purifying oil, you can extend its lifespan, minimize unscheduled downtime, and improve overall machine performance.
Performance Metric | Description |
---|---|
Improved Safety | Reduces the risk of mechanical failures and accidents. |
Less Frequent Oil Changes | Extends oil lifespan, lowering replacement and disposal costs. |
Reduced Unscheduled Downtime | Minimizes costly breakdowns caused by contaminated fluids. |
Better Machine Performance | Enhances equipment efficiency and ensures safer, more sustainable operations. |
These benefits make vacuum dehydration systems indispensable for industries relying on heavy machinery, such as automotive, aerospace, and food processing.
Hydraulic systems and lubrication systems
Hydraulic and lubrication systems require clean fluids to function effectively. Contaminated oil can lead to control issues, mechanical failures, and reduced equipment performance. Vacuum dehydration machines address these challenges by maintaining fluid purity, which improves safety, reduces maintenance costs, and enhances machine efficiency.
Benefit | Description |
---|---|
Improved Safety | Prevents mechanical failures and reduces accident risks. |
Less Frequent Oil Changes | Saves on replacement fluid and disposal costs. |
Less Unscheduled Downtime | Avoids production losses caused by machinery breakdowns. |
Better Machine Performance | Ensures optimal equipment operation and productivity. |
By investing in these systems, you can protect your hydraulic and lubrication systems from contamination, ensuring long-term reliability and cost savings.
Marine, mining, and other industries
Vacuum dehydration oil purification machines play a vital role in marine, mining, and other heavy-duty industries. These sectors rely on machinery that operates under extreme conditions, where oil contamination can lead to costly failures and downtime. By purifying oil, you ensure equipment reliability and extend its operational life.
Why oil purification matters in these industries
Marine and mining equipment often face harsh environments. Water contamination in oil is common due to humidity, leaks, or submersion. Solid particles from dirt and debris further degrade oil quality. Contaminated oil reduces lubrication efficiency, leading to wear and tear on critical components. Purifying oil prevents these issues, keeping your machinery running smoothly.
Tip: Regular oil purification reduces the risk of breakdowns, saving you time and money on repairs.
Key benefits for marine and mining operations
Vacuum dehydration systems offer several advantages for these industries:
- Enhanced Equipment Durability: Clean oil minimizes wear on engines, hydraulic systems, and gearboxes.
- Improved Operational Efficiency: Purified oil ensures smoother performance, reducing energy consumption.
- Lower Maintenance Costs: Fewer breakdowns mean less money spent on repairs and replacements.
- Environmental Compliance: Reusing purified oil helps meet sustainability goals and reduces waste.
Real-world applications
In marine operations, these machines purify lubricants used in ship engines and hydraulic systems. For mining, they maintain the quality of oils used in excavators, drills, and conveyor systems. Other industries, such as construction and agriculture, also benefit from these systems to keep their machinery in top condition.
By investing in vacuum dehydration oil purification machines, you protect your equipment, improve efficiency, and contribute to sustainable practices.
How to choose the right vacuum dehydration oil purification machine
Assessing oil type and compatibility
Start by identifying the type of oil you plan to purify. Different oils, such as hydraulic fluids, transformer oils, or turbine lubricants, have unique properties. Some oils may contain additives that require special handling. Check the machine’s specifications to ensure compatibility with your oil type.
Tip: Always verify the machine’s ability to handle the viscosity and temperature range of your oil. This ensures optimal performance and prevents damage to the equipment.
Compatibility also extends to the contaminants you need to remove. If your oil contains high levels of water or gas, choose a machine designed to handle these specific challenges.
Determining capacity and performance requirements
Evaluate your operational needs to determine the machine’s required capacity. Consider the volume of oil you need to process daily. Machines come in various capacities, ranging from small portable units to large industrial systems.
- Small-scale operations: Ideal for facilities with limited oil usage.
- Medium to large-scale operations: Suitable for industries requiring continuous oil purification.
Performance metrics like water removal efficiency, filtration precision, and processing speed are equally important. For example, if you need to reduce water content to below 10 ppm, select a machine with high dehydration efficiency.
Note: Overestimating capacity can lead to unnecessary costs, while underestimating it may cause delays in operations.
Evaluating maintenance needs and operational costs
Maintenance plays a crucial role in the long-term performance of your vacuum dehydration system. Look for machines with user-friendly designs that simplify filter replacement and routine servicing. Machines with automated controls and diagnostic features can reduce maintenance efforts.
Operational costs include energy consumption, filter replacements, and potential downtime. Compare models to find one that balances efficiency with affordability. Investing in a reliable machine may cost more upfront but saves money in the long run by reducing maintenance and operational expenses.
Pro Tip: Choose a machine with a proven track record of durability and low failure rates to minimize unexpected costs.
Considering additional features and customization options
When selecting a vacuum dehydration oil purification machine, additional features and customization options can significantly enhance its performance and usability. These features not only improve the purification process but also make the machine more user-friendly and efficient.
Key Features to Consider
Some advanced features can optimize your machine’s functionality. These include:
- Automated cleaning cycles: Reduce manual intervention and ensure consistent performance.
- Advanced filtration technologies: Provide higher precision in removing impurities.
- Digital monitoring systems: Allow you to track oil quality and machine performance in real-time.
- IoT integration: Enables remote monitoring and control, improving operational efficiency.
These features streamline operations and help you maintain oil quality with minimal effort.
Customization Options
Customization ensures the machine meets your specific needs. For example, you might require a machine with a higher capacity or one designed for a particular type of oil. Some popular customization options include:
Feature/Option | Description |
---|---|
Touchscreen HMI Control | Enhances user interface and control. |
Particle Counter | Improves monitoring of oil quality. |
Moisture Sensor | Detects moisture levels for better purification. |
These options allow you to tailor the machine to your operational requirements, ensuring optimal performance.
Compliance and Efficiency
It is essential to choose a machine that complies with local and international environmental regulations. This includes adhering to noise and emissions standards. Compliance not only ensures legal operation but also promotes energy efficiency and waste minimization. By selecting a machine with eco-friendly features, you contribute to sustainability while maintaining high purification standards.
Investing in the right features and customization options ensures your machine delivers maximum value. These enhancements improve efficiency, reduce maintenance efforts, and align with modern industrial needs.
Vacuum dehydration oil purification machines are essential for maintaining oil quality and extending the life of your equipment. By removing contaminants, these machines ensure your machinery operates efficiently and reliably. They also reduce maintenance costs and minimize downtime, making them a cost-effective solution for industrial operations.
You can also contribute to environmental sustainability by reusing purified oil and reducing waste. When selecting a machine, evaluate your specific needs, such as oil type, capacity, and additional features. This careful assessment ensures you choose the best solution for your operations.
FAQ
What types of oils can a vacuum dehydration oil purification machine process?
These machines can handle a wide range of oils, including transformer oils, hydraulic fluids, turbine lubricants, and gear oils. Always check the machine’s specifications to ensure compatibility with your specific oil type and its viscosity range.
How often should you use a vacuum dehydration oil purification machine?
The frequency depends on your operational needs and oil contamination levels. For critical equipment, regular purification every few weeks ensures optimal performance. Monitor oil quality using tests like water content and particle count to determine the ideal schedule.
Can you operate the machine continuously?
Yes, most machines are designed for continuous operation. Some models can run for over 100 hours without interruption. However, regular maintenance and monitoring are essential to ensure consistent performance and prevent wear.
Is it possible to customize a vacuum dehydration oil purification machine?
Many manufacturers offer customization options. You can add features like moisture sensors, advanced filtration systems, or IoT integration for remote monitoring. Customization ensures the machine meets your specific operational and environmental requirements.
How does using this machine benefit the environment?
By purifying and reusing oil, you reduce waste and minimize the need for new oil production. This process conserves resources, lowers your carbon footprint, and helps meet environmental regulations, promoting sustainable industrial practices.