Vacuum pumps play a vital role in oil purification by ensuring machinery operates reliably and efficiently. Contaminated oil can cause severe equipment damage, leading to costly repairs. Industries increasingly rely on vacuum dehydration oil purification systems (VDOPS) to address this issue. These systems, valued at $1.2 billion in 2023, are projected to grow at a 10.5% CAGR, reflecting their importance in maintaining clean oil and reducing operational costs. By removing contaminants effectively, vacuum pumps help you extend machinery lifespan and minimize downtime.
Key Takeaways
- Vacuum pumps clean oil faster by removing dirt quickly. This helps machines work better and last longer.
- Using vacuum pumps lowers costs and makes oil and machines last longer, saving money over time.
- Clean oil from vacuum pumps stops damage to machines. This improves how they work and cuts down on breaks.
Efficiency Gains in Oil Purification
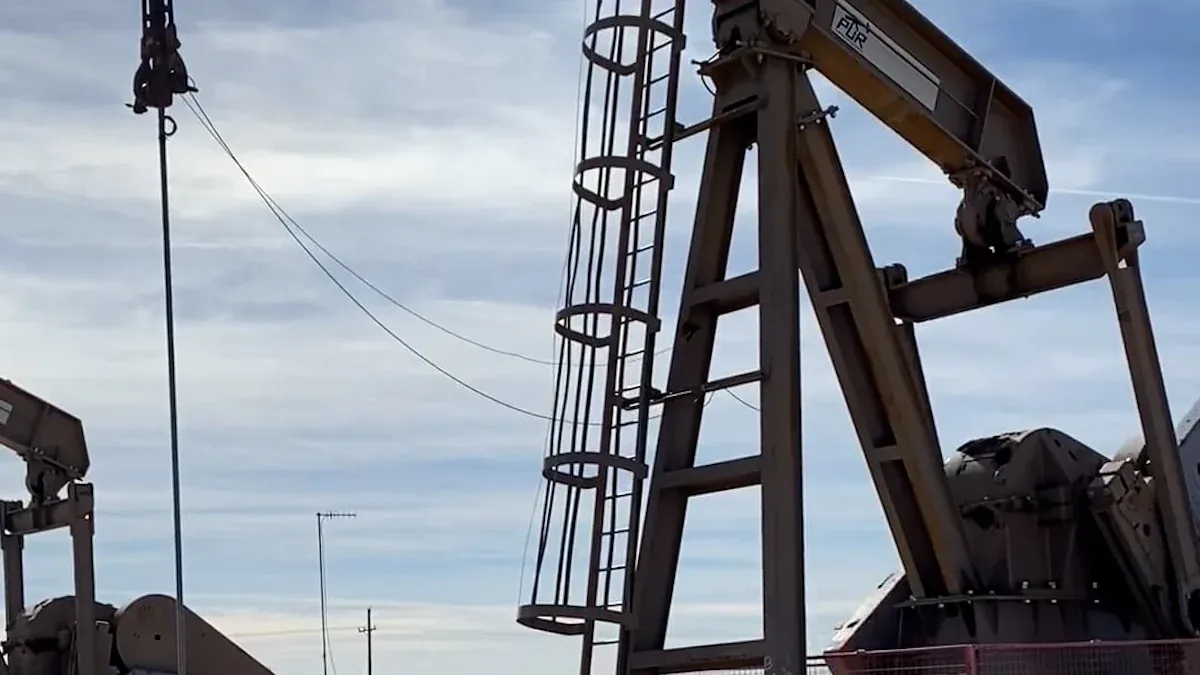
Accelerated removal of contaminants
Vacuum pumps speed up the process of removing contaminants from oil. By creating a low-pressure environment, these pumps allow impurities like dirt, sludge, and debris to separate more efficiently. This rapid removal ensures that your oil purification system operates at peak performance. Faster contaminant extraction also reduces the risk of equipment damage, helping you maintain reliable machinery operation.
Superior moisture and gas extraction
Moisture and gas can significantly degrade oil quality. Vacuum pumps excel at extracting these unwanted elements, ensuring cleaner oil for your machinery. For example, tests on different pipe types show consistent vacuum pressure transitions, regardless of wall thickness or inner diameter:
Pipe Type | Wall Thickness (mm) | Inner Diameter (mm) | Vacuum Pressure Transition |
---|---|---|---|
Test Pipe-A | 1.65 | 6.2 | Similar transitions observed |
Test Pipe-B | 14 | 6.0 | Similar transitions observed |
This consistency highlights the effectiveness of vacuum pumps in maintaining oil purity, even under varying conditions.
Minimized system downtime
Vacuum pumps reduce downtime by improving system reliability. Fixed service intervals for newer pump models range from 4 to 6 months, ensuring fewer interruptions. Additionally, reliable pump performance minimizes unexpected failures, which can otherwise lead to extended downtime and costly clean-up operations. By integrating vacuum pumps into your oil purification process, you can keep your machinery running smoothly and avoid unnecessary delays.
Cost-Effectiveness of Vacuum Pump Systems
Reduced operational expenses
Vacuum pumps help you cut operational costs by improving the efficiency of oil purification processes. Their ability to purify oil quickly and effectively reduces waste and energy consumption, which directly impacts your bottom line. For example:
- Energy-efficient vacuum systems lower energy expenses, as noted by the U.S. Department of Energy.
- Companies adopting these systems often see enhanced competitiveness due to reduced costs.
- Quick purification processes also minimize waste, contributing to environmental sustainability.
Ripple Road Maple, a manufacturing company, reported significant savings on energy bills after switching to an energy-efficient Becker pump. This change not only reduced electrical costs but also increased production capacity, boosting profitability. By investing in vacuum pump systems, you can achieve similar financial benefits while supporting sustainable practices.
Extended oil and equipment lifespan
Vacuum pumps extend the lifespan of both oil and machinery by maintaining oil purity. Cleaner oil reduces wear and tear on equipment, ensuring longer service intervals and fewer breakdowns. This means you spend less on repairs and replacements. Additionally, the improved performance of your machinery leads to higher productivity. Over time, these benefits translate into substantial cost savings.
Energy-efficient technology
Energy consumption accounts for nearly 50% of a vacuum pump’s total lifespan cost. Advanced vacuum pump systems are designed to minimize this expense. For instance, energy-efficient models consume significantly less power, reducing lifetime energy costs, which can be five times the initial purchase price. Maintenance costs, which make up about 30% of the total cost, are also lower due to the reliability of modern systems. By choosing energy-efficient vacuum pumps, you not only save money but also reduce your environmental footprint.
Vacuum pumps are a smart investment for oil purification. They lower operational expenses, extend equipment lifespan, and utilize energy-efficient technology to maximize cost-effectiveness.
Enhanced Oil Quality and System Performance
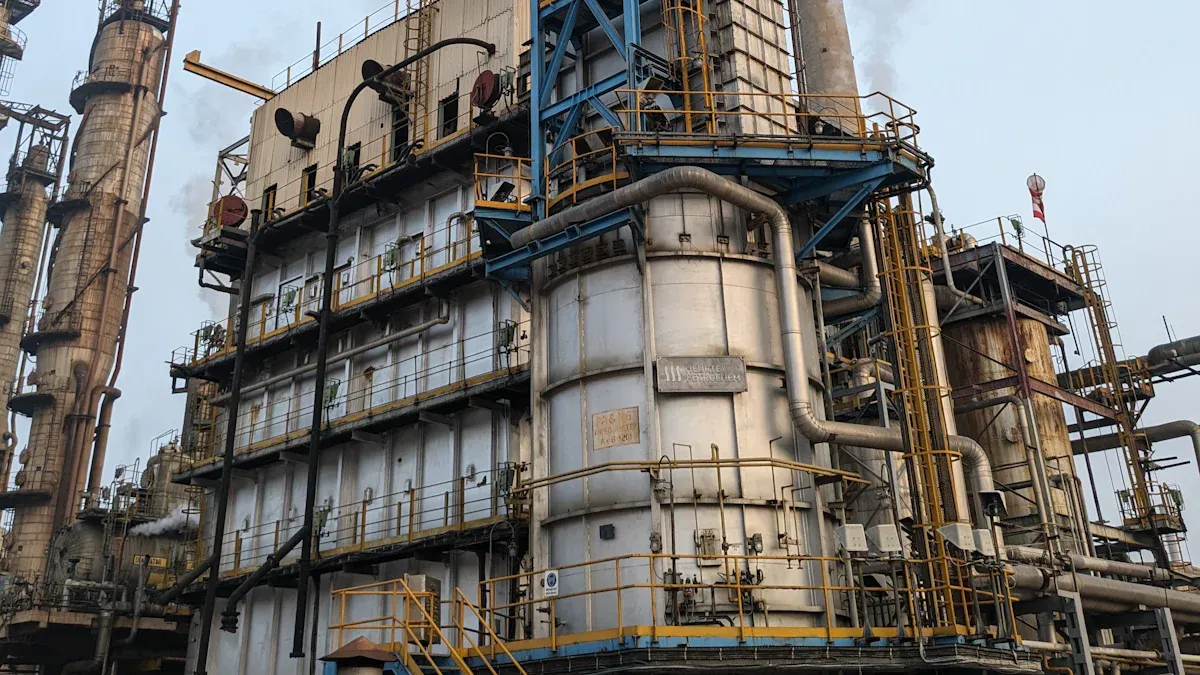
Consistent oil purity for optimal machinery function
Vacuum pumps ensure consistent oil purity, which is essential for keeping your machinery running at its best. Clean oil reduces friction and prevents the buildup of harmful deposits. This leads to smoother operations and fewer interruptions. When oil purification systems use vacuum pumps, they remove contaminants more effectively. This process maintains the oil’s integrity, allowing your equipment to perform reliably even under demanding conditions.
Prevention of wear and tear on equipment
Contaminated oil accelerates wear and tear on machinery. Vacuum pumps play a critical role in preventing this by extracting moisture, gases, and other impurities. Cleaner oil minimizes the abrasive effects on moving parts, extending the lifespan of your equipment. For example, industries using vacuum pump systems report fewer breakdowns and longer service intervals. By reducing mechanical stress, you can save on repair costs and avoid unexpected downtime.
Reliable results in high-demand applications
Vacuum pumps deliver reliable results, even in high-demand industrial scenarios. Their advanced technology ensures consistent performance, making them ideal for critical processes. Consider the following metrics that highlight their reliability:
Metric | Description |
---|---|
Energy Efficiency | Newer models reduce energy consumption, enhancing operational cost-effectiveness. |
Maintenance Costs | Predictive maintenance sensors decrease maintenance frequency and costs by approximately 25%. |
Cost of Downtime | Downtime in critical processes can lead to losses exceeding $100,000 per hour, emphasizing reliability. |
These features make vacuum pumps indispensable for industries where precision and efficiency are non-negotiable. By integrating them into your oil purification system, you can achieve consistent results and maintain peak productivity.
Vacuum pumps offer three key benefits: efficiency, cost-effectiveness, and improved performance. They ensure cleaner oil, which protects your machinery and extends its lifespan. By integrating vacuum pumps, you can reduce downtime and enhance productivity. Explore solutions designed for your needs to achieve reliable results and maintain optimal oil quality.